Destylator przemysłowy to urządzenie, które odgrywa kluczową rolę w procesach separacji substancji chemicznych. Działa na zasadzie różnicy temperatur wrzenia poszczególnych składników mieszaniny, co pozwala na ich oddzielenie. W praktyce proces destylacji polega na podgrzewaniu cieczy do momentu, w którym zaczyna ona parować. Para następnie jest schładzana i kondensowana z powrotem do stanu ciekłego, co umożliwia zbieranie oczyszczonego produktu. Destylatory przemysłowe są wykorzystywane w wielu branżach, takich jak przemysł chemiczny, petrochemiczny czy spożywczy. W zależności od zastosowania, mogą mieć różne konstrukcje i rozmiary, od małych jednostek laboratoryjnych po ogromne instalacje przemysłowe. Dzięki zaawansowanej technologii, nowoczesne destylatory są w stanie osiągać wysoką efektywność oraz jakość uzyskiwanych produktów, co jest niezwykle istotne w kontekście konkurencyjności na rynku.
Jakie są rodzaje destylatorów przemysłowych
W świecie przemysłowym istnieje wiele różnych typów destylatorów, które różnią się konstrukcją oraz zastosowaniem. Najpopularniejsze z nich to destylatory prostoliniowe oraz frakcyjne. Destylatory prostoliniowe są najprostsze w budowie i najczęściej stosowane do separacji cieczy o znacznej różnicy temperatur wrzenia. Z kolei destylatory frakcyjne są bardziej skomplikowane i umożliwiają separację składników o zbliżonych temperaturach wrzenia dzięki zastosowaniu kolumny frakcyjnej. W tej kolumnie para przechodzi przez szereg kondensatorów i odparowywaczy, co pozwala na wielokrotne skraplanie i parowanie substancji, a tym samym ich skuteczniejsze oddzielanie. Innym rodzajem są destylatory próżniowe, które działają w obniżonym ciśnieniu, co pozwala na destylację substancji w niższej temperaturze. To szczególnie ważne dla substancji wrażliwych na wysokie temperatury. Oprócz tego istnieją również destylatory azeotropowe oraz membranowe, które znajdują zastosowanie w bardziej specjalistycznych procesach przemysłowych.
Jakie są zastosowania destylatorów przemysłowych
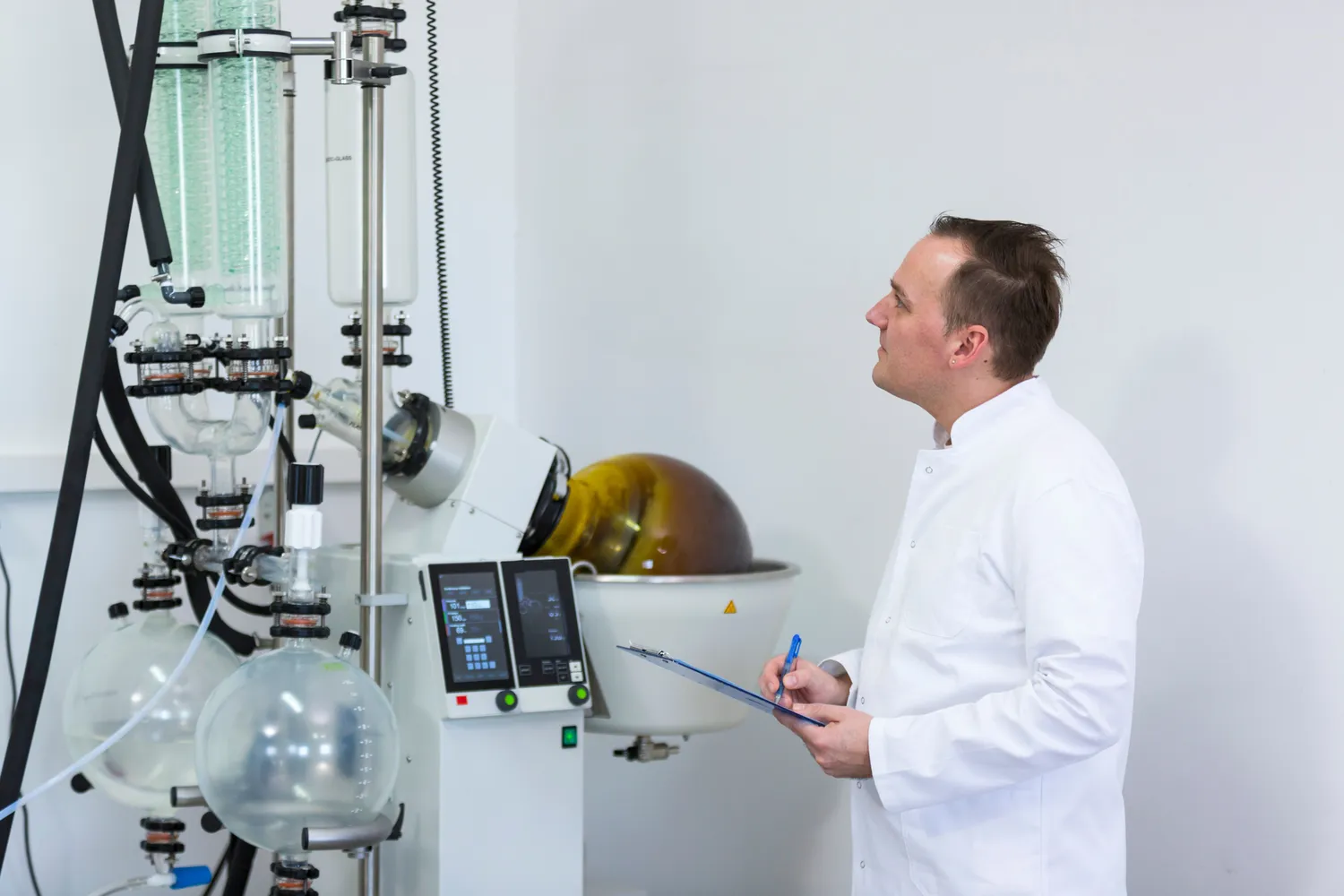
Destylatory przemysłowe mają szerokie zastosowanie w różnych branżach, co czyni je niezbędnym elementem wielu procesów produkcyjnych. W przemyśle chemicznym służą do oczyszczania surowców oraz produkcji różnych chemikaliów, takich jak alkohole czy kwasy organiczne. W przemyśle petrochemicznym wykorzystuje się je do separacji frakcji ropy naftowej, co pozwala na uzyskanie paliw oraz innych produktów naftowych. Destylacja jest również kluczowym procesem w produkcji napojów alkoholowych, gdzie służy do uzyskiwania czystego alkoholu z fermentowanych surowców. W przemyśle spożywczym destylatory są wykorzystywane do produkcji olejków eterycznych oraz ekstraktów smakowych. Ponadto coraz częściej stosuje się je w recyklingu rozpuszczalników oraz innych substancji chemicznych, co przyczynia się do ochrony środowiska i zrównoważonego rozwoju.
Jakie są korzyści z używania destylatorów przemysłowych
Korzystanie z destylatorów przemysłowych przynosi wiele korzyści zarówno dla producentów, jak i dla środowiska naturalnego. Przede wszystkim umożliwiają one uzyskiwanie wysokiej jakości produktów poprzez skuteczne oddzielanie niepożądanych składników oraz zanieczyszczeń. Dzięki temu możliwe jest zwiększenie efektywności produkcji oraz redukcja strat surowców. Destylatory przyczyniają się także do oszczędności energetycznej poprzez optymalizację procesów technologicznych. Nowoczesne urządzenia charakteryzują się zaawansowanymi systemami sterowania oraz monitorowania, co pozwala na bieżąco dostosowywać parametry pracy do zmieniających się warunków produkcji. Ponadto stosowanie destylacji jako metody oczyszczania substancji chemicznych ma pozytywny wpływ na ochronę środowiska poprzez zmniejszenie ilości odpadów oraz emisji szkodliwych substancji do atmosfery.
Jakie są najnowsze technologie w destylacji przemysłowej
W ostatnich latach rozwój technologii destylacyjnych w przemyśle przeszedł znaczną ewolucję, co przyczyniło się do zwiększenia efektywności i jakości procesów produkcyjnych. Nowoczesne destylatory przemysłowe często wykorzystują zaawansowane systemy automatyzacji, które pozwalają na precyzyjne kontrolowanie parametrów pracy, takich jak temperatura, ciśnienie czy przepływ. Dzięki temu możliwe jest osiągnięcie optymalnych warunków dla procesu destylacji, co przekłada się na wyższą jakość uzyskiwanych produktów. Wiele nowoczesnych urządzeń wyposażonych jest w inteligentne algorytmy, które analizują dane w czasie rzeczywistym i dostosowują parametry pracy w celu maksymalizacji wydajności. Innym istotnym trendem jest zastosowanie technologii membranowych, które oferują alternatywę dla tradycyjnej destylacji. Membrany umożliwiają selektywne oddzielanie składników na podstawie ich rozmiaru lub właściwości chemicznych, co może prowadzić do oszczędności energii oraz zmniejszenia emisji zanieczyszczeń. Ponadto coraz częściej stosuje się techniki destylacji z wykorzystaniem ultradźwięków czy mikrofal, które mogą znacznie przyspieszyć proces separacji.
Jakie są wyzwania związane z używaniem destylatorów przemysłowych
Mimo licznych korzyści płynących z używania destylatorów przemysłowych, istnieje również szereg wyzwań, które muszą być brane pod uwagę przez producentów. Jednym z głównych problemów jest konieczność stałego monitorowania i konserwacji urządzeń, aby zapewnić ich prawidłowe działanie oraz uniknąć awarii. Niewłaściwe ustawienia parametrów pracy mogą prowadzić do obniżenia jakości produktów oraz zwiększenia kosztów produkcji. Kolejnym wyzwaniem jest zarządzanie odpadami powstającymi w wyniku procesów destylacyjnych. Wiele substancji chemicznych może być szkodliwych dla środowiska, dlatego konieczne jest wdrażanie skutecznych metod ich utylizacji lub recyklingu. Dodatkowo, zmieniające się regulacje prawne dotyczące ochrony środowiska oraz bezpieczeństwa pracy mogą wymuszać na przedsiębiorstwach dostosowywanie swoich procesów produkcyjnych do nowych norm. W kontekście globalnej konkurencji firmy muszą także inwestować w innowacje technologiczne oraz szkolenie pracowników, aby utrzymać swoją pozycję na rynku.
Jakie są koszty związane z inwestycją w destylatory przemysłowe
Inwestycja w destylatory przemysłowe wiąże się z różnorodnymi kosztami, które należy dokładnie przeanalizować przed podjęciem decyzji o zakupie. Koszt zakupu samego urządzenia może być znaczny i zależy od jego rodzaju oraz specyfikacji technicznych. Na przykład, nowoczesne destylatory frakcyjne mogą kosztować znacznie więcej niż prostoliniowe ze względu na bardziej skomplikowaną konstrukcję i dodatkowe funkcje. Oprócz samego zakupu należy uwzględnić również koszty instalacji oraz uruchomienia urządzenia, które mogą obejmować prace budowlane oraz dostosowanie infrastruktury zakładu do nowych wymagań technologicznych. Kolejnym istotnym elementem są koszty eksploatacyjne, takie jak zużycie energii elektrycznej oraz materiałów eksploatacyjnych potrzebnych do działania destylatora. Warto również pamiętać o kosztach związanych z konserwacją i serwisowaniem urządzenia, które mogą być regularnie wymagane w celu zapewnienia jego prawidłowego funkcjonowania. Dodatkowo przedsiębiorstwa muszą brać pod uwagę potencjalne straty wynikające z przestojów produkcyjnych spowodowanych awariami lub koniecznością przeprowadzania napraw.
Jakie są przyszłe kierunki rozwoju technologii destylacyjnej
Przemysł destylacyjny stoi przed wieloma możliwościami rozwoju technologii w nadchodzących latach. Jednym z kluczowych kierunków jest dalsza automatyzacja procesów produkcyjnych, co pozwoli na zwiększenie efektywności i redukcję błędów ludzkich. Inwestycje w sztuczną inteligencję oraz uczenie maszynowe mogą umożliwić lepsze prognozowanie wydajności procesów oraz szybsze reagowanie na zmiany warunków pracy. Kolejnym ważnym trendem jest rosnące zainteresowanie technologiami ekologicznymi i zrównoważonym rozwojem. Przemysł będzie dążył do minimalizacji wpływu na środowisko poprzez wdrażanie bardziej efektywnych metod separacji oraz recyklingu surowców i odpadów. W miarę wzrostu znaczenia odnawialnych źródeł energii można spodziewać się większego wykorzystania energii słonecznej czy geotermalnej w procesach destylacyjnych. Również rozwój materiałów o lepszych właściwościach izolacyjnych może przyczynić się do obniżenia kosztów energetycznych związanych z działaniem destylatorów. Wreszcie, globalizacja rynku sprawi, że firmy będą musiały dostosować swoje technologie do różnych regulacji prawnych oraz oczekiwań klientów na różnych rynkach międzynarodowych.
Jakie są najlepsze praktyki dotyczące obsługi destylatorów przemysłowych
Aby zapewnić prawidłowe działanie i maksymalną wydajność destylatorów przemysłowych, kluczowe jest stosowanie najlepszych praktyk dotyczących ich obsługi i konserwacji. Przede wszystkim operatorzy powinni być odpowiednio przeszkoleni w zakresie obsługi urządzeń oraz znajomości procesów chemicznych zachodzących podczas destylacji. Regularne kontrole stanu technicznego sprzętu są niezbędne do wykrywania potencjalnych usterek zanim staną się one poważnym problemem. Ważne jest również monitorowanie parametrów pracy urządzenia, takich jak temperatura czy ciśnienie, aby szybko reagować na wszelkie nieprawidłowości. Utrzymanie czystości wewnętrznych elementów destylatora ma kluczowe znaczenie dla jakości uzyskiwanych produktów; dlatego regularne czyszczenie i konserwacja powinny być standardową procedurą operacyjną. Dodatkowo warto prowadzić dokumentację wszystkich działań związanych z obsługą urządzeń, co pozwala na analizę danych i identyfikację obszarów wymagających poprawy.